Fermenter Achieves Well-ferment @
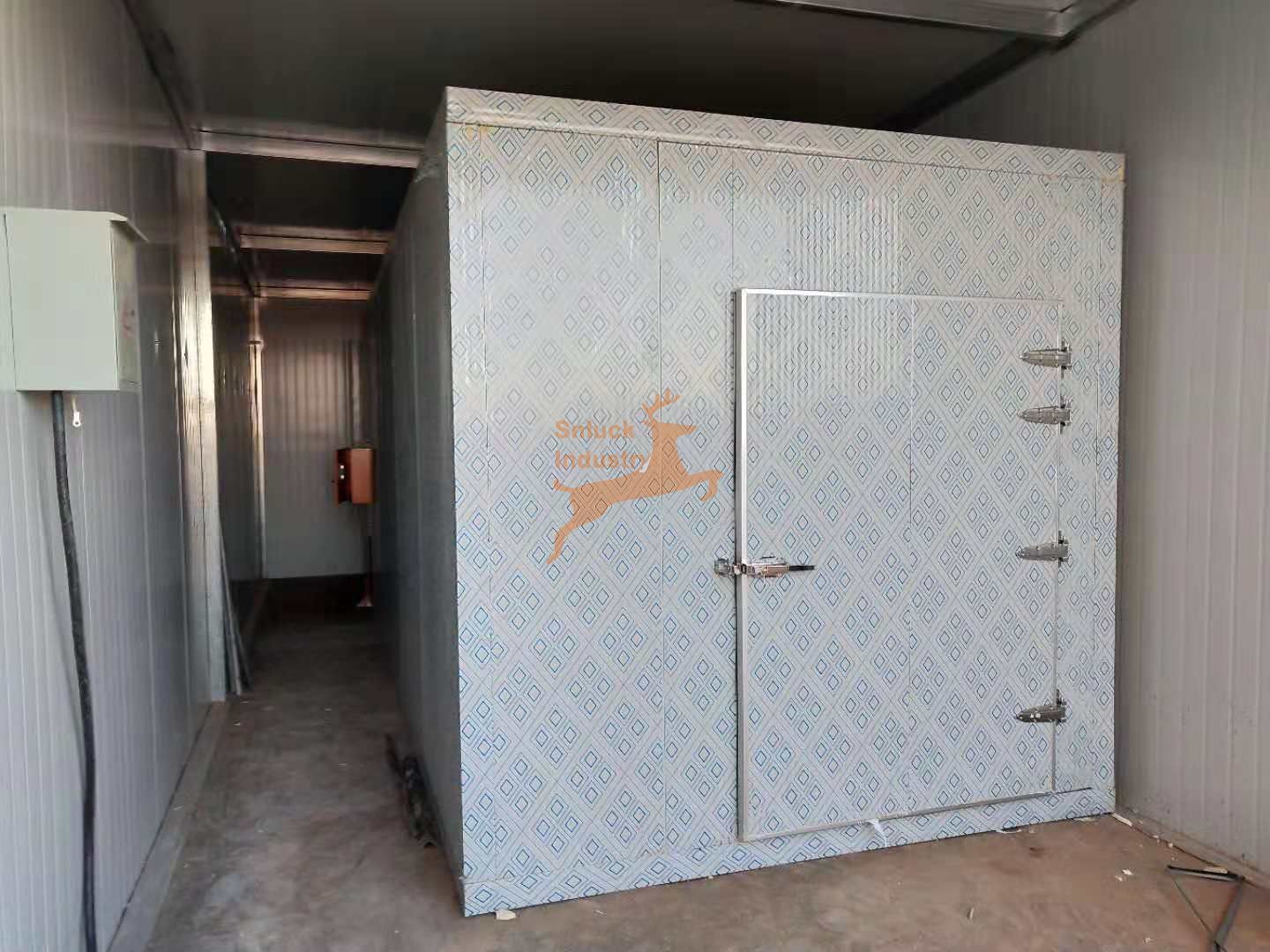
- 1
High Yield: Achieves a single-batch fermentation output of 1000 kilograms of solid products.
- 2Dynamic Oxygen Supply Parameters: Oxygen Concentration Control: 12-18%, Turning Frequency: 2-24 times per day.
- 3
Static Sealing Parameters: CO2 Concentration Monitoring: ±0.5%, Pressure Relief Valve Setting.
- 4
High Biomass Concentration: Capable of reaching a biomass concentration of 15 g/L (dry cell weight) for yeast fermentation.
- 5
High Substrate Conversion Rate: Boasts a substrate conversion rate of up to 85% for glucose utilization in a specific fermentation process.
- 6
High Product Purity: Ensures a product purity of over 95% for a certain enzyme product, minimizing the cost and difficulty of subsequent separation and purification processes.
- 7
Stable Fermentation: Maintains excellent fermentation stability with production indicators fluctuating within a range of ±5% across multiple batches.
- 8
Low Contamination Rate: Keeps the contamination rate as low as 1% through strict aseptic protection systems, minimizing production losses caused by contamination.
- 9
Precise Parameter Control: Offers accurate control over various parameters such as temperature (±0.5℃), pH (±0.2), dissolved oxygen (±5% of the set value), etc., creating an optimal environment for fermentation.
- 10
Comprehensive Functionality: Equipped with features like automatic feeding, online detection (able to monitor parameters in real-time with an accuracy of 98%), CIP (Clean-in-Place) which can clean the equipment within 30 minutes, SIP (Sterilize-in-Place) that can complete sterilization in 60 minutes.
MBD Module
72-hour Installation Time & 300% Capacity ScalabilityPlug & Play Module
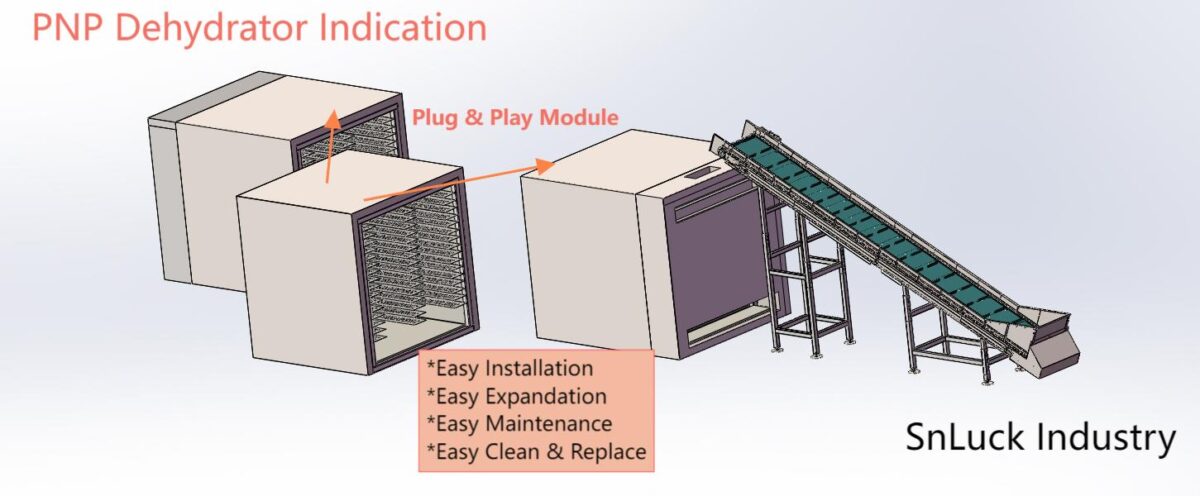
IOT Control
Max Throughput: 13.2t/h | Energy Use: 1.08kW·h/kgIntime Monitering Data
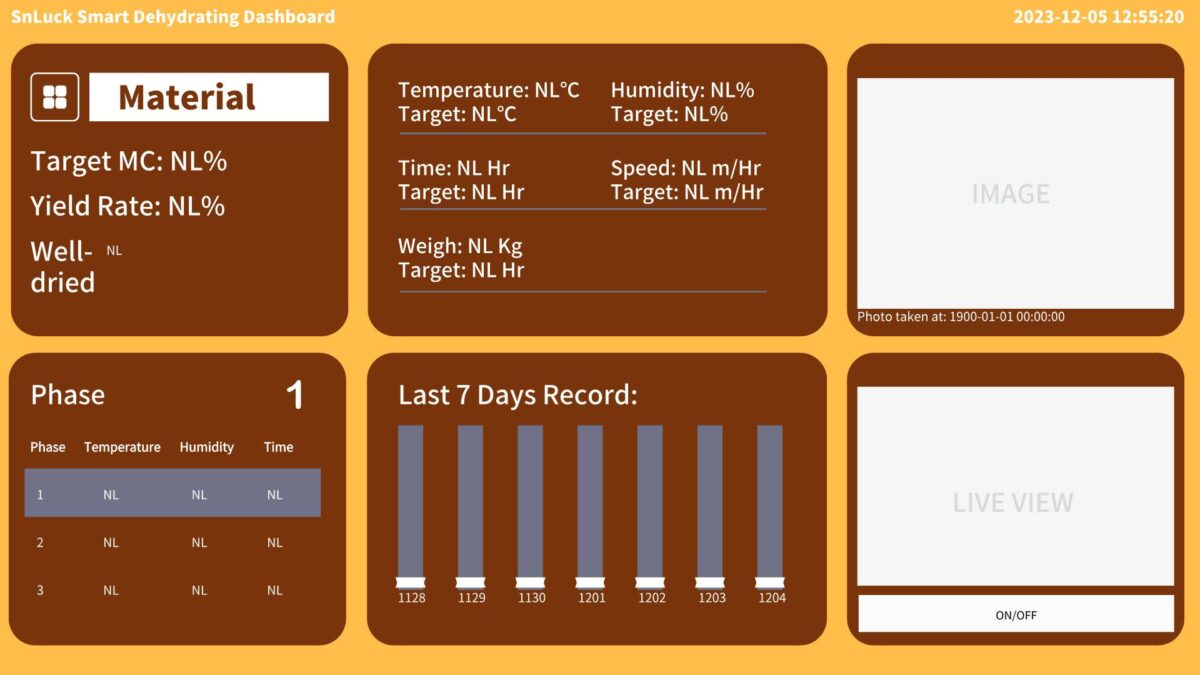
Holistic Line
OPC UA | Profinet | EtherCAT | All 7 Process JointFull Process Production
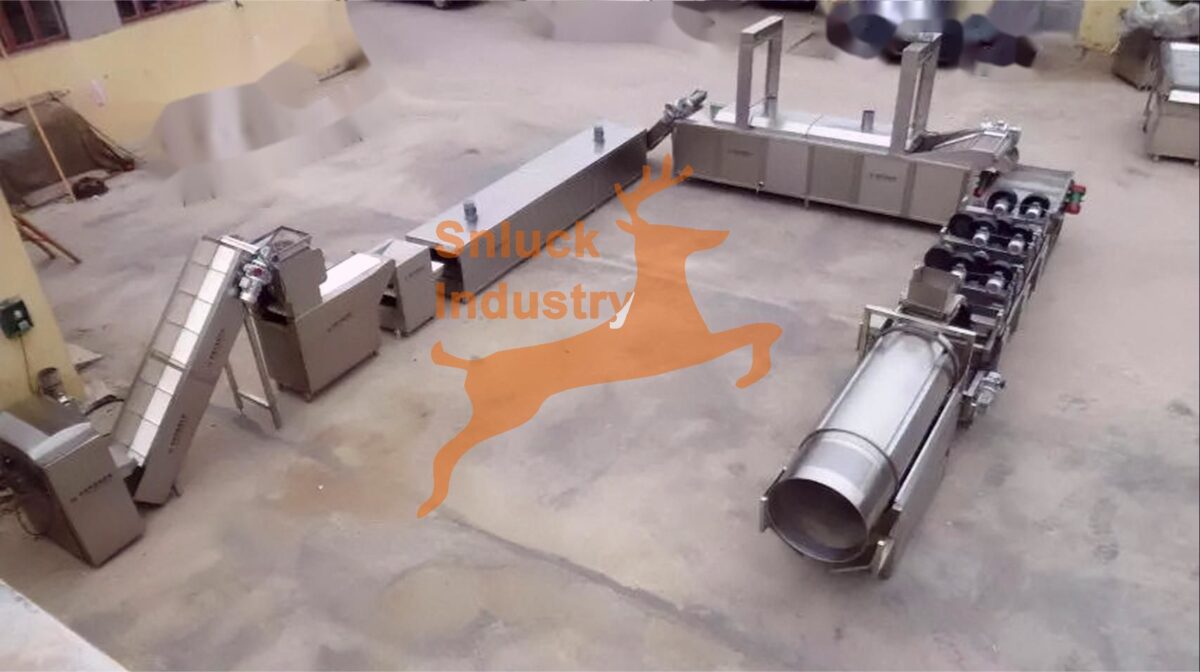
Components of Fermenter -
Structure Module
Outstanding Function of Fermenter -
5 Supreme capabilities
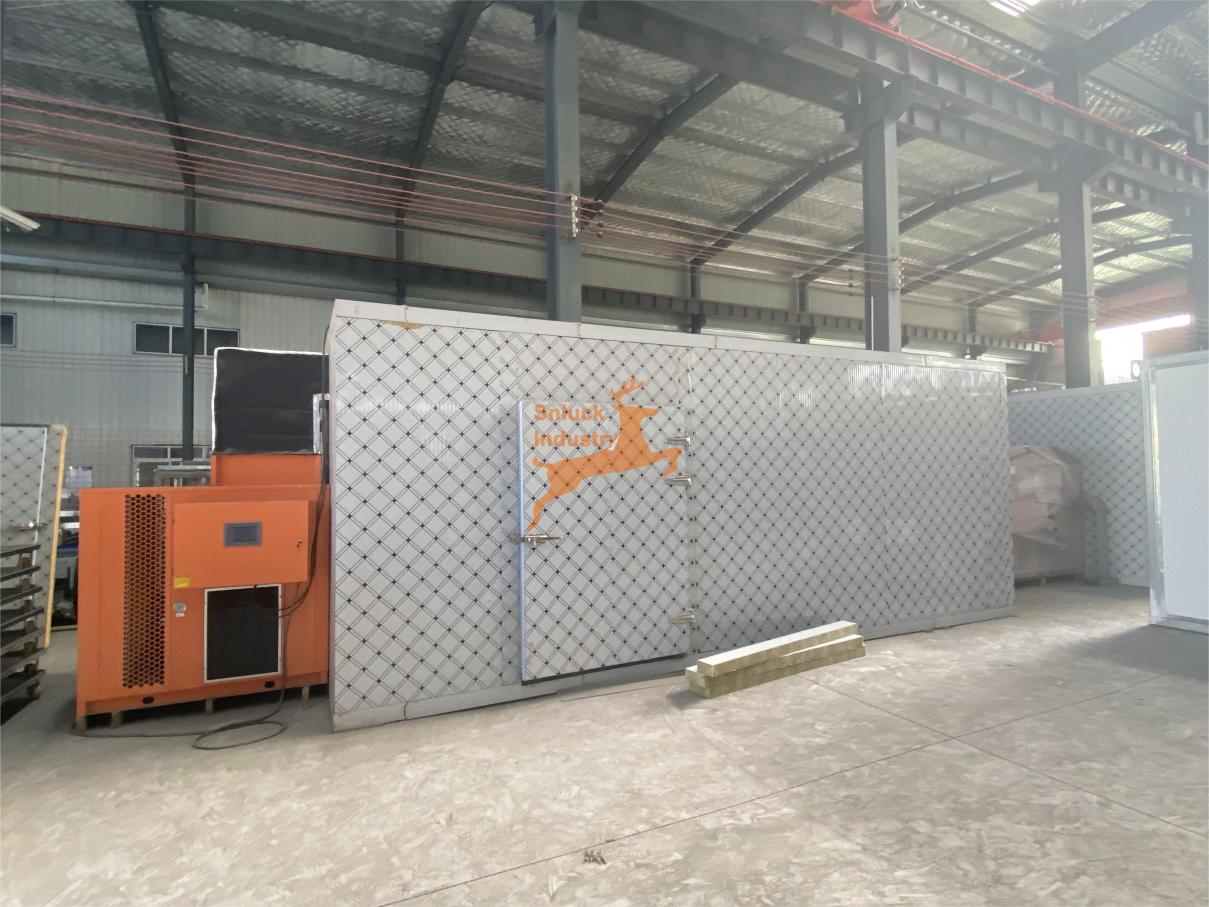
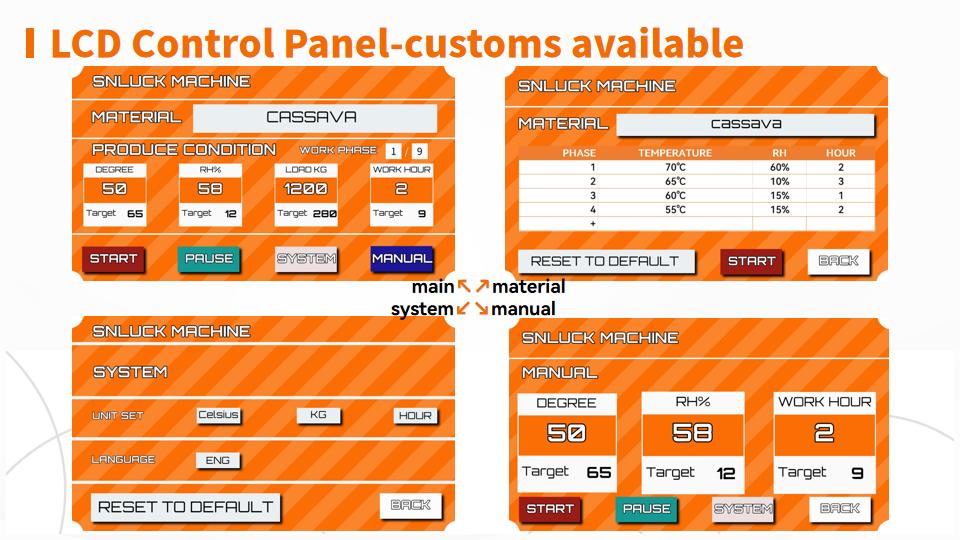
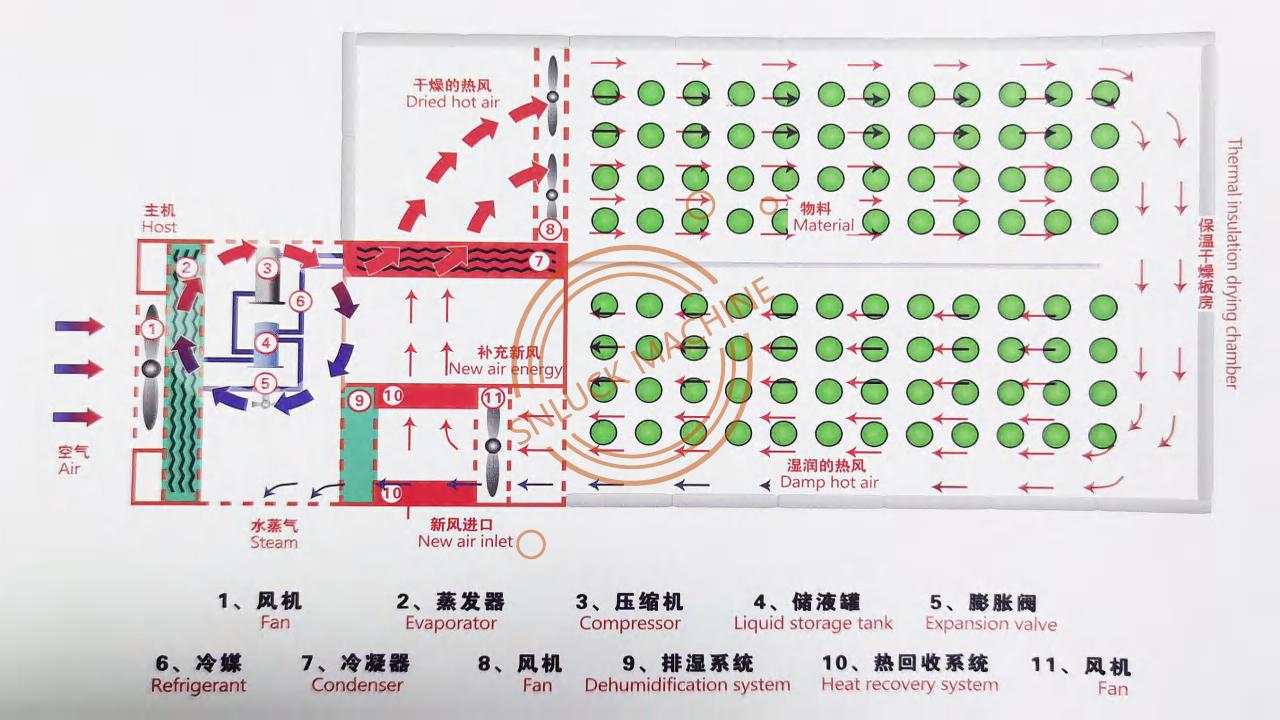
- Reduced Energy Consumption and Operating Costs
- Lower Environmental Impact (reduced carbon footprint)
- Improved Process Efficiency and Product Quality
- Enhanced Equipment Durability and Uptime
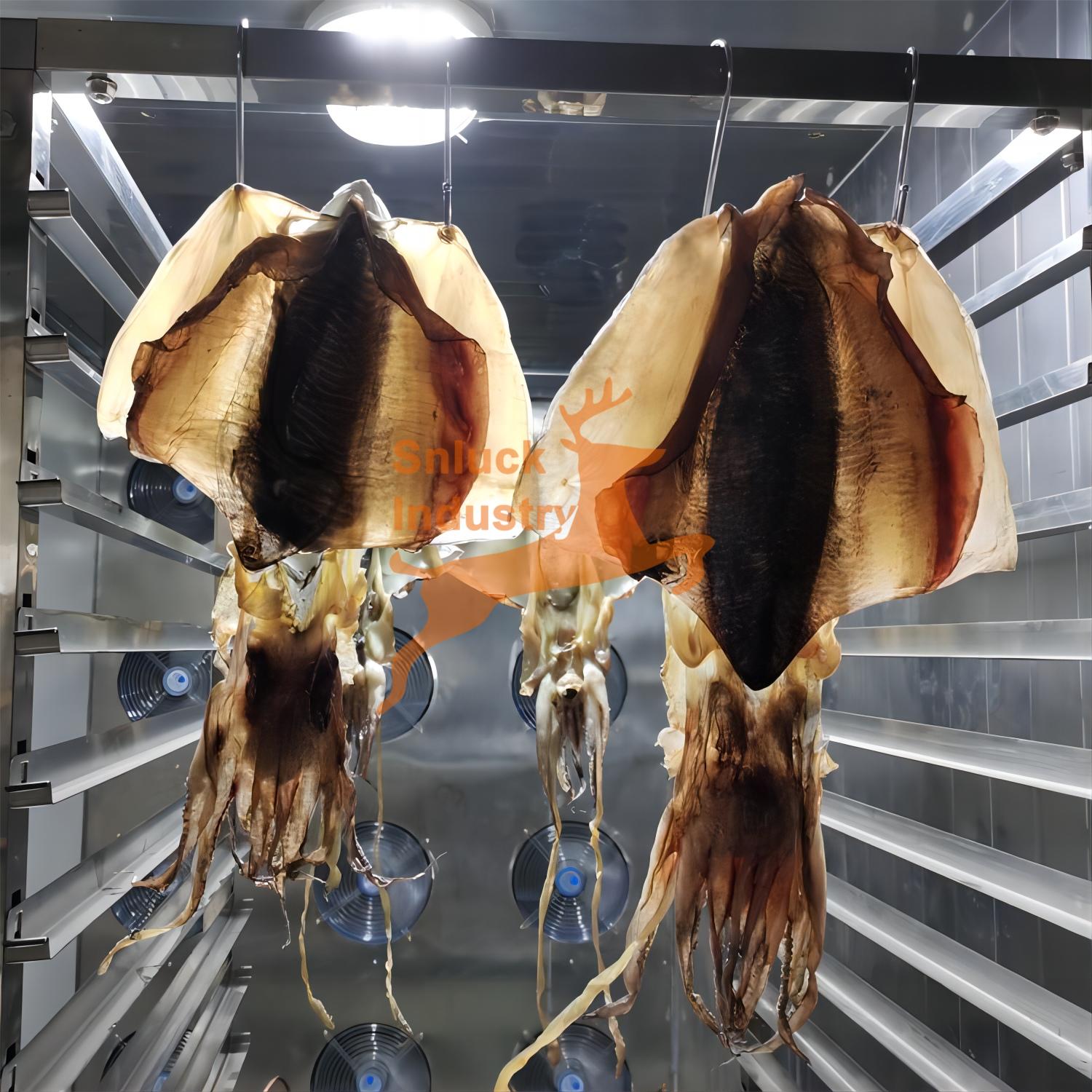
- Increased productivity: Continuous operation without human intervention maximizes output.
- Reduced labor costs: Eliminates the need for constant on-site staffing.
- Consistent quality: Ensures uniform production standards as processes are not affected by human variations.
- 24/7 operation: Allows for around-the-clock production, meeting tight deadlines and increasing output.
- Enhanced safety: Minimizes human exposure to potentially hazardous production environments.
- Optimal resource utilization: Based on real-time data from sensors, resources like energy and raw materials are used more efficiently.
- Faster decision-making: Data collected via IoT enables quick analysis and informed decisions for process improvement.
- Remote monitoring and control: Allows management to oversee production from anywhere, providing flexibility and prompt response to issues.
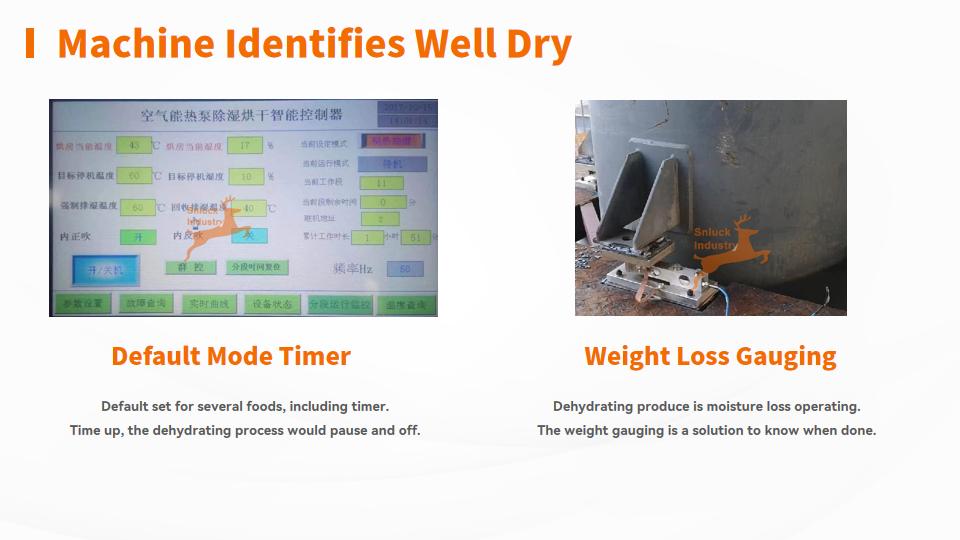
- Informed decision-making: Enables users to make strategic decisions based on accurate and detailed historical data.
- Process optimization: Identifies areas for improvement by analyzing production patterns and trends.
- Quality control: Helps maintain consistent product quality by tracking and comparing data over time.
- Predictive maintenance: Anticipates equipment failures by monitoring data patterns, reducing downtime.
- Traceability: Allows for easy tracking of production batches for quality and compliance purposes.
- Performance evaluation: Measures the efficiency and productivity of the production process.
- Cost analysis: Enables better understanding of production costs and identification of cost-saving opportunities.
- Proof of compliance: Provides evidence of meeting regulatory and industry standards.